The 10 step Universal Troubleshooting Process
1. Prepare
2. Make damage control plan
3. Get a complete and accurate symptom description
4. Reproduce the symptom
5. Do the appropriate corrective maintenance
6. Narrow it down to the root cause
7. Repair or replace the defective component
8. Test
9. Take pride in your solution
10. Prevent future occurrence of this problem
Troubleshooting Tips and Articles
• Logic for Troubleshooting
o Tools and Solutions
o Superstition, Positive Thinking and Luck
o The Many Faces of Troubleshooting and Problem Solving
o Litt's Process Hypothesis
o Speculation, Guesswork and Prayer
o Generic Problem Solving With the Universal Troubleshooting Process
o A great demo of Divide and Conquer
• Universal Troubleshooting Process
o Troubleshooting tips
o Common troubleshooting myths
o Gavin Gray
o Team Troubleshooting
o When the Going Gets Tough
o Natural Born Troubleshooters
o Do the Easy Ones First
o Courseware FAQ
• Industry Specific Information
o Recruiters and Consulting Firms
o Training Firms
• Handy Troubleshooting Tactics
o Corrective Maintenance
o Bottleneck Analysis
o Exploiting Perceived Similarities
o Simplify Everything
o Distinctions and Commonalities
o Damage Control
o Preventive Maintenance
o Shotgunning
• The Attitude
o The Attitude
o Take Pride
o When the Going Gets Tough
o Troubleshooting, Luck and Superstition
o Team Troubleshooting
o Natural Born Troubleshooters
o Take Pride
• Intermittents
o About intermittents
o Intermittents
o My favorite Intermittent Stories
o NASA's Intermittent
• Toolsmanship
o Toolsmanship
o Choosing the Right Tool
Here Are Some Other Troubleshooting Tips:
Quality Control
The quality of the solution depends on the quality put into the steps. Getting a complete and accurate symptom description, and reproducing the symptom, assures that you fix the symptom the customer wanted you to fix. A good damage control plan ensures that you won't make anything worse. Correct general maintenance shows the customer you care about quality, and often greatly reduces costs. A correct narrowing process will reduce costs, prevent further damage, and ensure that the root cause, rather than a peripheral symptom, is fixed. Proper repair or replacement of the defective component prevents further damage.
Testing is like inspection in the factory. The few defects that escape the quality controls of the earlier steps are caught here, by showing that the symptom description you recorded and reproduced has been eliminated, and that no further problems have been created. Taking pride is a periodic maintenance item that ensures the quality of you as a troubleshooter and a human being. Preventing further occurrence is the utmost in customer service. The quality of the solution depends on the quality of the steps.
Bottleneck analysis
Use this when the symptom can be described as "it's too (slow, fast, etc.)". Bottleneck is a special kind of Divide and Conquer (see step 6). One cool and easy bottleneck analysis test is to slow down a section of the system. If that section is the bottleneck, the system as a whole will slow down significantly. If not, it won't. The entire March 1998 Troubleshooting Professional Magazine is devoted to bottleneck analysis.
Don't skip steps
The Divide and Conquer process can be thought of as continually forcing the problem into ever smaller boxes, until it's trapped. Some of the worst troubleshooting debacles I've seen involved the problem escaping the box. In other words, the troubleshooter thought he had proved it was in one area, when it was really in another. When that happens, tests become inconclusive and the troubleshooter starts to doubt himself. Whole days can be wasted. Take every precaution to avoid this -- don't skip steps.
c klAngex..jigz jigz
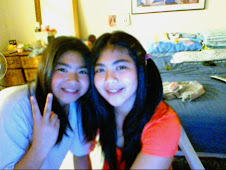
wafA jod ni ako idol oh..
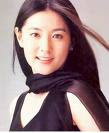
Wednesday, February 24, 2010
Tuesday, January 20, 2009
Monday, January 19, 2009
Monday, January 12, 2009
Thursday, December 11, 2008
Wednesday, November 5, 2008
Subscribe to:
Posts (Atom)